What are Vertical Broach Machines?
- Patrick
- 2021年9月8日
- 讀畢需時 3 分鐘
Imagine you wanted to cut a star pattern inside a round tube. What would be the efficient way to do it? How about 10,000+ times? Turns out broaches are the best way to do it. Broaching is the process of producing a none circular shape in a part. Think of a hex bolt, the hex shape is made with a broach. Broaching can be performed on a lathe, mill or a dedicated broaching machine. Vertical and horizontal broaching machines produce keyways or internal cuts through parts. Let’s learn about vertical broach machines. They are specialty machines used for high volume production parts.
A broach is the actual cutting tool. There are different types of broaches, ranging from keyway broaches that cut one area at a time to custom broaches which cut an entire internal shape. A keyway broach has teeth that increase in length/cut along its shaft or length. Think of a broach as a staircase each step brings you closer to the top of the stairs. In this case the top of the stairs is the broaches full cut. The broaches we use are spline broaches, which are designed to cut keyways for attaching spiders to bicycle wheel hubs.
Using a Vertical Broach Machine:
The broach is held above the work area. Our operator places the parts to be cut, (bicycle spiders in our case) into a fixture. The broach is lowered into the center of the work holder, It then engages with the bottom half of the vertical broaching machine. Coolant is then turned on and the broach is pulled through the part. As the broach passes through the part it slices away layer after layer until the final dimensions are met. When the operator has removed the newly cut parts they hit a button and the broach is pushed back up engaging with the top lifting mechanism. It’s then lifted back to the upper starting position and awaits the operator's input.
Simple process right? Let’s see what it actually takes to get to the button push.

The Setup:
Let’s get a broach, turns out broaches can’t be bought at the local hardware store. We source the actual broach as engineering and machining them requires specialty equipment and expertise.
While we are waiting on our broach to arrive we need to come up with a way to keep our parts in position. We will engineer and machine a fixture. The fixture is how we hold the actual parts and are often customized to each individual part. I’m going to walk you through this process.
Making a Fixture, The Base:
A slug is inserted into a lathe. The part is turned removing the center material as well as creating a lip for inserting the jig to the broach machine. The part is flipped to remove outer material leaving a protruding center ring. The picture below is both the upper and lower fixture after being turned on a lathe.
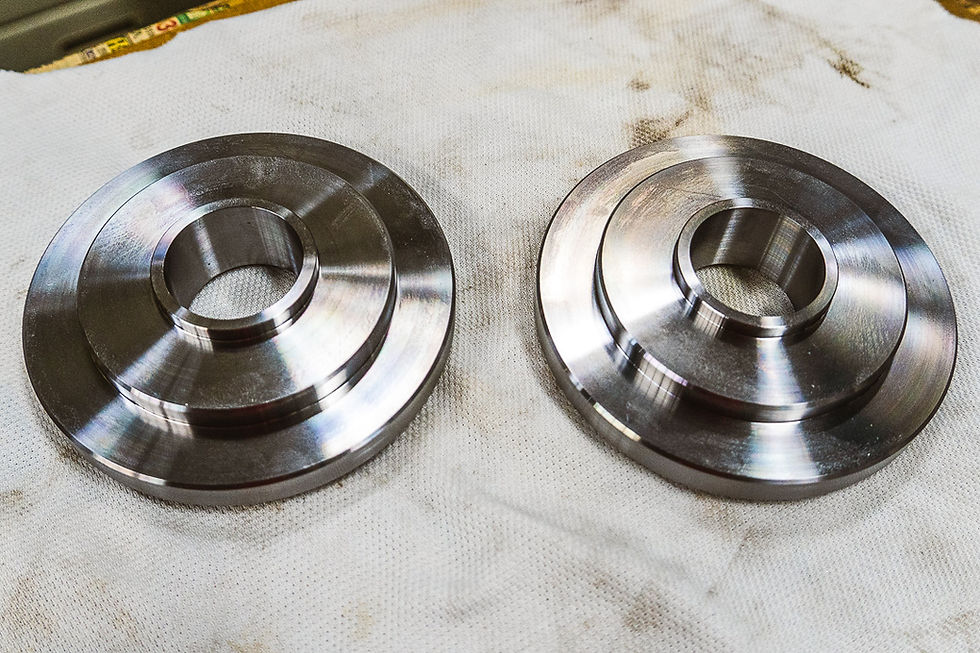
Let’s move to the mill for operation two. We machine slots for fastening, alignment and adjustment. Then there are tapped inner holes that are used to mount the topper piece that holds the parts. On the outer circle of the fixture an alignment flat is also milled. This will be done two more times, one for each spider size.
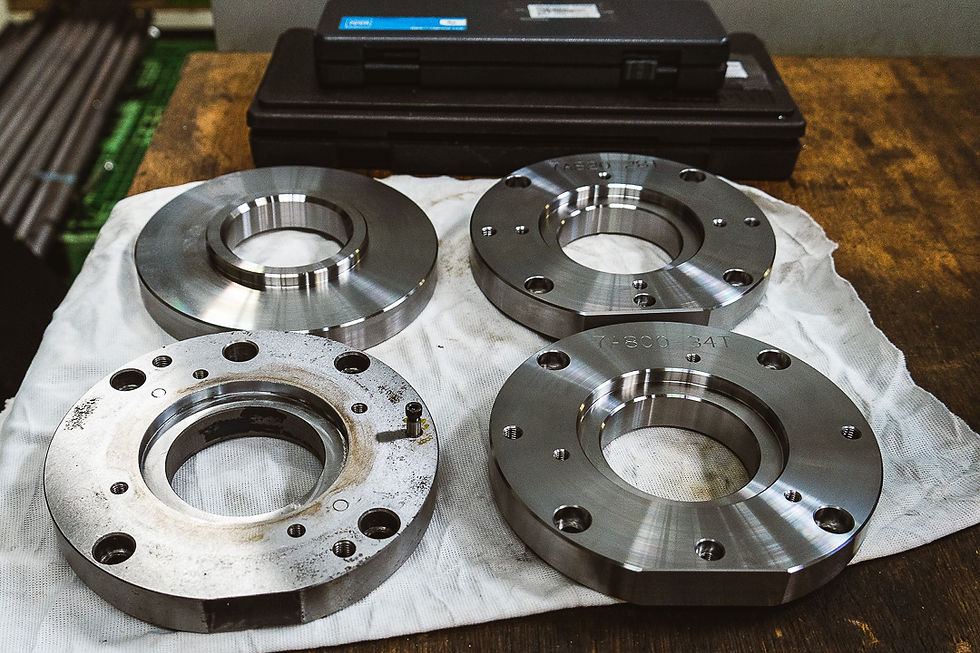
Making a Fixture, The Topper:
The next step is to finish up the top fixture. This part follows the same basic operations as the larger base disk just at a smaller diameter. The center is removed and a negative mating lip is turned to insert onto the base plate. We will also machine some pins and pegs; they are turned then threaded on a lathe.
We took those parts to the mill for op two. Next we drilled and tapped holes for securing to the jig. A few holes are drilled and tapped for pins that will align the part. Larger holes are drilled for pegs that keep the part secured during the broaching process. Some of the pegs are shorter to mate with the spiders outer feature. The fixture is flipped and a notch is cut, this allows us to separate the base and topper. We mill flats on the sides of the pegs. The pins will also get milled.
The Take-away: Vertical broaches are specialty tools for manufacturing keyways at high volume. They are extremely useful if you're manufacturing bicycle components or complex internal features. The process of creating fixtures and jigs to set up the machines is a lengthy process. However, once the fixtures are in place it’s just a matter of repeating the broaching process 5,000+ times.
Contact us to learn how vertical broaches can be used to manufacture your parts. If you have any corrections or resources for us to improve please comment below.
Comments